Shattering Bottlenecks in Ammonia Production
New material supplies electrons to quickly disrupt nitrogen bond, speeding up the reaction
(April 2015)
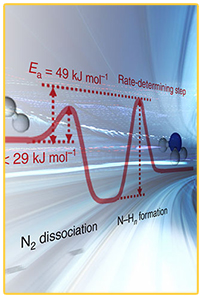
Scientists discovered how to remove a key roadblock and speed the synthesis of ammonia, which would reduce the cost of ammonia production and make the manufacturing process safer. Enlarge Image.
Results: One stretch of bad traffic can slow the whole journey. It's the same for chemical reactions. To break through the bottleneck for ammonia synthesis, scientists on three continents worked together to find a better way. A new electron-rich material, supporting a ruthenium-based catalyst, supplies electrons so fast that it dramatically speeds up what was once the slowest step: decoupling nitrogen atoms in a molecule of nitrogen (N2).
"The research shows that one can enhance ruthenium catalytic activity by using a properly selected supporting material -- and the result is a change of the reaction bottleneck," said Dr. Peter Sushko, who worked on the study in collaboration with the team of experimentalists led by Prof. Hideo Hosono at Tokyo Institute of Technology. Sushko conducts research and manages the Materials Sciences group at Pacific Northwest National Laboratory.
Why It Matters: Ammonia is synthesized in massive quantities for use in crop fertilizers. The process used today, known as the Haber-Bosch process, was invented in 1909 and developed to the industrial scale in 1913. The challenge is the first step, which only happens under extreme pressure. Reducing the need for high pressures here would reduce the cost of ammonia production and make the manufacturing process safer. Also, it could simplify ammonia synthesis enough to allow it to be a fuel, packing energy from wind turbines and solar cells inside its bonds.
"Scientists have been looking for catalysts to speed the rate of ammonia production for decades," said Sushko. "Now, we have a catalyst that lowers the activation energy for the first step in the reaction so much that it is no longer the bottleneck."
Methods: The study looks at refining the Haber-Bosch process, where nitrogen gas (N2) is broken into two nitrogen ions. Each ion then takes on, one at a time, three hydrogen atoms. As a result, each molecule of nitrogen gas leads to two molecules of ammonia (NH3).
The team replaced the traditional iron-based catalyst with one made of ruthenium. However, the key was creating a specialized calcium- and aluminum-based support. Using this support, abbreviated 12CaO⋅7Al2O3 (or C12A7), they characterized and analyzed the support using both experiments and models.
They discovered that the support feeds the catalyst extra electrons. The catalyst uses the electrons to rip apart the nitrogen without the need for high pressures. With the support, the reaction works at 0.1 MPa. Sans support, ammonia synthesis requires pressures between 20 to 40 MPa.
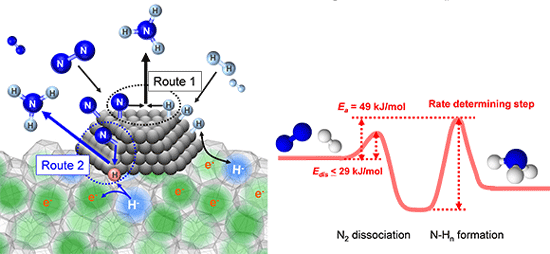
A zoo of elementary processes leading to the formation of ammonia at ruthenium nanoparticles supported on the electron-rich C12A7 substrate. The substrate can release and take in electrons and hydrogen species to facilitate the reaction. The image was created by the authors, published in Nature Communications, and is provided under Creative Commons license.
With the insights from the research, scientists can look for cheaper materials and use similar ammonia synthesis steps. Or, they can take the support and optimize it to run faster, shifting the focus of researchers to the reaction's second step, nitrogen hydrogenation.
"The work was made possible by the highly collaborative, long-running, use-inspired projects from ACCEL, sponsored by the Japan Science and Technology Agency, Ministry of Education, Culture, Science and Technology, and the Japanese government," said Sushko.
What's Next? At PNNL, Sushko and two postdoctoral fellows, Dr. Lewis Johnson and Dr. Phuong-Vu Ong, are continuing computational studies, working together with experimentalists Prof. Masaaki Kitano and Prof. Hideo Hosono at Tokyo Institute of Technology to understand and control these electron-supplying materials, which have applications as a catalytic support and in electronics.
Acknowledgments
Sponsors: All of the authors, except P.V.S., were funded by the Funding Program for World-Leading Innovative R&D on Science and Technology (FIRST) and by a fund from ACCEL of Japan Science and Technology Agency. P.V.S was supported by a Laboratory Directed Research and Development project at PNNL. H.H. proposed an idea of this subject and M.H. and H.H. directed the entire project. M.K., S.K., and Y.I. performed the synthesis, characterization, and catalytic testing of the support. P.V.S. and N.K carried out ab initio calculations. All authors discussed the results and commented on the study. M.K, M.H., P.V.S., and H.H. wrote the manuscript.
Facilities: Computing facilities of HECToR and ARCHER, via the team's membership of the United Kingdom's High-Performance Computing Materials Chemistry Consortium, funded by the Engineering and Physical Sciences Research Council (Grant EP/L000202).
Research Team: Masaaki Kitano, Shinji Kanbara, Yasunori Inoue, Tokyo Institute of Technology; Navaratnarajah Kuganathan, University College London; Peter V. Sushko, Pacific Northwest National Laboratory and Japan Science and Technology Agency; Toshiharu Yokoyama, Michikazu Hara, and Hideo Hosono, Tokyo Institute of Technology and Japan Science and Technology Agency
Reference: Kitano M, S Kanbara, Y Inoue, N Kuganathan, PV Sushko, T Yokoyama, M Hara, and H Hosono. 2015. "Shifting the Bottleneck in Ammonia Synthesis: Electride-Supported Ru Catalyst Boosts N2 Dissociation." Nature Communications 6, article 6731. DOI: 10.1038/ncomms7731