Stories of Discovery and Innovation-
Ladies and Gentlemen, Start Your Engines
Fundamental studies in catalysis enabled the use of efficient "lean-burn" engines for vehicle transportation.
(March 2011)
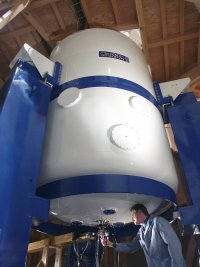
900-MHz NMR spectrometer allows scientists to transcend previous limits in catalyst characterization. Enlarge Image
What's that coming out of your exhaust pipe, trucker? If you have an older rig, one of those tailpipe emissions will be NOx, a mixture of nitric oxide and nitrogen dioxide. NOx pollutes the air and reacts with other chemicals to form smog and ozone. It can be a serious health risk.
Many of today's vehicles have significantly reduced NOx because of U.S. Department of Energy research. DOE has been critical in creating the fundamental understanding needed to effectively remove NOx emissions from engine exhaust. In recent years, DOE research has been focused on solving the vexing issues that have been preventing the fuel efficient lean-burn engine from becoming a commercial reality for today's vehicles. Lean-burn engines operate at very high air-to-fuel ratios and, in this way, can improve fuel efficiency by more than 25 percent over standard gasoline engines. Unfortunately, these higher ratios mean that emission control devices developed for standard gasoline engines are not effective for removing NOx.
The story starts with Pacific Northwest National Laboratory's catalysis research program, sponsored by the Department of Energy's Office of Science, which supports a substantial research program in catalysis, and later by the Office of Energy Efficiency and Renewable Energy's Vehicle Technology program. In conducting the research, the unique suite of tools in EMSL, a DOE national scientific user facility also funded by the Office of Science and located at PNNL, was crucial.
Not all catalysts are created equal, so understanding the fundamental chemistry of catalytic reactions is critical in developing the most efficient and effective materials. Catalysts are materials that help chemical reactions take place rapidly and efficiently without actually being used up in the reaction. Essentially, they "loan" a part of their molecular structure to the reaction and then return to their original state when the reaction is complete. Catalysts are used in many processes, ranging from the manufacture of pharmaceuticals to industrial oil refining for producing fuels and petrochemicals.
At PNNL, early research explored the way rhodium catalysts clean up NOx emissions in the conventional catalytic converters for today's gasoline-powered vehicles. This research examined the structural sensitivity of the catalytic reaction that converts NOx to the benign molecule, nitrogen. Like a lock and key, if a catalyst lock has the right structure when the chemical key is inserted, everything fits and the reaction works. If the lock and key don't quite match, then the reaction can take place but with undesirable products. The PNNL research showed that the best catalyst structure was achieved when rhodium catalyst particles were small and had rough surfaces. If the rhodium particles became too large, nitrous oxide was formed instead of nitrogen.
The BES-funded research led to a better understanding of how the catalyst functions and enabled improvements in conventional catalytic converters.
Based on PNNL's record of success, Cummins, Inc., an engine manufacturer, and Johnson Matthey, a supplier of catalysts, approached the Laboratory for help in developing catalyst solutions for removing NOx emissions from lean-burn engines, such as diesels. Cummins and Johnson Matthey engineers were studying a new material that provided the foundation for a new catalyst technology—Lean-NOX Trap.
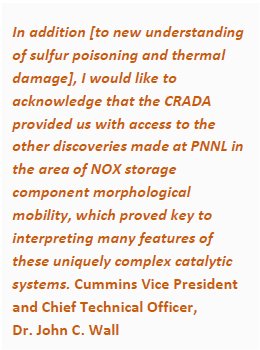
The Cummins lean-burn diesel-powered engine was destined for powerful vehicles, like the Dodge Ram pickup truck. Because the current catalytic converters were not effective for emissions from these engines, they could not meet the new emissions standards for diesel vehicles. So, with the dual impacts of cleaner air and greater fuel efficiency hanging in the balance, new and significantly improved catalyst technologies were a necessity.
Simply stated, the new Lean-NOX Trap material worked fine initially, but it did not last. The answers to why the material failed too early would require unique fundamental studies of the catalytic materials and reactions involved, typically beyond the scope of companies whose expertise lies in product engineering.
In 2003, with funding from the DOE's Vehicle Technologies Program, Cummins and PNNL began a collaborative, multi-year Cooperative Research and Development Agreement—or CRADA—to explore the Lean-NOX Trap material failures with the support of an integrated suite of unique scientific instruments in EMSL.
Like any good mystery, the outcomes were surprising and challenged the way scientists think about how catalysts function.
Initial investigations focused on understanding the normal operation of the catalyst in the new technology. Part of what makes a catalyst a catalyst is that it supposedly is unchanged by the chemical reaction it is helps create. But the PNNL researchers discovered that, at least for Lean-NOX Trap systems, the catalyst changes greatly. As the catalyst's barium oxide component was storing and converting NOX, the catalyst was growing and shrinking on macroscopic scales, morphing from nanoparticle sizes to orders-of-magnitude bigger. Unfortunately, these useful and regularly recurring changes also were accompanied by some irreversible changes that caused permanent loss of Lean-NOX Trap performance.
But what were these harmful changes in the catalyst and how could they be prevented?
Researchers found the answer in the new data provided by a suite of EMSL instruments. In particular, EMSL's ultra-high field NMR spectroscopy provided the key to understanding the ways that the catalyst materials, barium oxide and platinum, interacted with the catalyst support material, aluminum oxide. The one-of-a-kind NMR in EMSL generated the highest-resolution chemical information (spectra) ever obtained for an aluminum oxide material, and the first quantitative, atomic-scale measurements of how the aluminum oxide support interacted with the LNT catalytic materials, platinum and barium oxide. PNNL scientists determined that the strengths of these interactions were responsible for both the desirable and undesirable catalyst changes during Lean-NOX Trap operation.
Armed with this new fundamental understanding of the important materials interactions in the Lean-NOX Trap catalysts, Cummins and Johnson Matthey developed improved materials and new ways of operating the diesel engines that minimized the harmful catalyst changes in the Lean-NOX Trap technology. Lean-NOX Trap technology was first used in the 2007 Dodge Ram pickup. The technology is now also being used on other fuel efficient diesel vehicles in the U.S. market, including the Volkswagen Jetta TDI.
The mystery was solved but the story has not ended. There are still many catalysis unknowns that could make for cleaner exhaust from more fuel efficient vehicle engines.
Big challenges include developing new scientific instruments that can observe catalyst structural changes while the chemical reactions take place and new computational approaches to simulate these very complex chemical and physical changes under conditions that are present in the real world. Such scientific advances are the engines for the next technological advances that will provide much greater fuel economy in our transportation sector without adversely impacting our environment.
Key contributors to this body of work were Dr. Ja Hun Kwak, Dr. Do Heui Kim, Dr. Charles Peden and Dr. Janos Szanyi, all of the Institute for Integrated Catalysis at Pacific Northwest National Laboratory.
Funding: Basic Research: DOE Office of Science, Office of Basic Energy Sciences
Scientific User Facility (Environmental Molecular Science Laboratory): DOE Office of Science, Office of Biological and Environmental Research
Follow-on Applied R&D: DOE Office of Energy Efficiency and Renewable Energy, Vehicle Technologies Program
Publications: Peden CHF, DN Belton, and SJ Schmieg. 1995. "Structure Sensitive Selectivity of the NO-CO Reaction over Rh(110) and Rh(111)." Journal of Catalysis 155(2):204-218. DOI:10.1006/jcat.1995.1204.
Szanyi J, JH Kwak, J Hanson, C Wang, T Szailer, and CHF Peden. 2005. "Changing Morphology of BaO/Al2O3 during NO2 Uptake and Release." Journal of Physical Chemistry B 109(15): 7339-7344. DOI:10.1021/jp044160z.
Kim DH, Y-H Chin, GG Muntean, A Yezeretz, NW Currier, WS Epling, H-Y Chen, H Hess, and CHF Peden. 2006. "Relationship of Pt Particle Size with the NOx Storage Performance over Thermally Aged Pt/BaO/Al2O3 Lean NOx Trap Catalysts." Industrial & Engineering Chemistry Research 45(26):8815-8821. DOI:10.1021/ie060736q.
Kwak JH, JZ Hu, DH Kim, J Szanyi, and CHF Peden. 2007. "Penta-coordinated Al3+ Ions as Preferential Nucleation Sites for BaO on γ-Al2O3: An Ultra-High Magnetic Field 27Al MAS NMR Study." Journal of Catalysis 251(1):189-194. DOI:10.1016/j.jcat.2007.06.029.
Kwak JH, JZ Hu, D Mei, C-W Yi, DH Kim, CHF Peden, LF Allard, and J Szanyi. 2009. "Coordinatively Unsaturated Al+3 Centers as Binding Sites for Active Catalyst Phases: Strong Interactions Between Pt and γ-Al2O3 Surfaces." Science 325(5948):1670-1673. DOI:10.1126/science.1176745.
Kwak JH, RG Tonkyn, DH Kim, J Szanyi, and CHF Peden. 2010. "Excellent Activity and Selectivity of Cu-SSZ-13 in the Selective Catalytic Reduction of NOx with NH3." Journal of Catalysis 275(2):187-190. DOI:10.1016/j.jcat.2010.07.031.
Related links: Pacific Northwest National Laboratory